In diesem Artikel möchten wir kurz auf das DMS-Messprinzip und vor allem auf die Anwendung DMS-basierter Sensoren eingehen. Da wir uns in erster Linie mit Prüftechnik für die Produktentwicklung und Qualitätssicherung befassen, sollen diese Anwendungsbereiche dabei im Vordergrund stehen. Der Artikel hat nicht den Anspruch als umfassende technische Dokumentation zu dienen und soll in erster Linie Einsteigern und Anwender einen Überblick über die Technik zu verschaffen. Wer etwas tiefer in die Materie einsteigen möchte, findet am Ende des Artikels dazu eine kleine Linksammlung mit weiterführenden Informationen.
Aufbau und Wirkungsweise von DMS-basierten Sensoren
Ein DMS (Dehnungsmessstreifen oder auch englisch Strain Gauge) ist zuerst einmal ein elektrisches Messgerät, das in der Lage ist Dehnungen oder Stauchungen in verschiedenenen Materialien zu messen. Die Struktur des Sensors besteht aus einem dünnen Metalldraht oder einer Metallfolie, die auf eine flexible Trägerschicht aufgebracht wird. Dabei wird versucht durch einen mäanderförmigen Aufbau eine möglichst große Länge kompakt unterzubringen. Wenn der Sensor einer Dehnung ausgesetzt ist, verformt sich die Metalleinlage zusammen mit der Trägerschicht und verändert dadurch ihren elektrischen Widerstand.
Dieser Effekt kann in der Praxis mit Hilfe einer sogenannten Brückenschaltung ausgenutzt und gemessen werden. Dabei wird zunächst eine Speisespannung – zum Beispiel eine Gleichspannung von 5 oder 10 Volt – angelegt. Die Veränderung des elektrischen Widerstandes kann dann gemessen und elektronisch weiterverarbeitet werden. Dabei sind die reinen elektrischen Größen alleine zunächst nicht besonders aussagekräftig, sondern müssen in verwertbare Informationen umgerechnet und in Relation gebracht werden. Dazu später mehr.
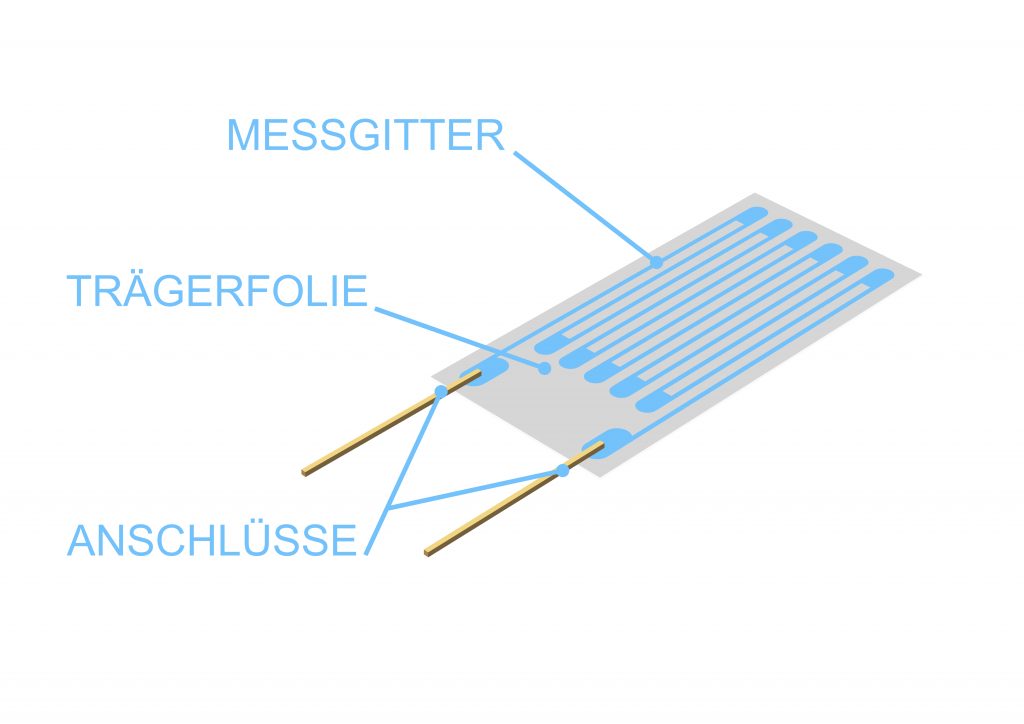
Praktische Umsetzung des Prinzip DMS
Wir kennen jetzt das zugrundeliegende Funktionsprinzip eines Dehnungsmessstreifens. Um das Ganze jedoch sinnvoll als Sensor und somit Messinstrument nutzen zu können, müssen noch weitere wichtige Schritte erfolgen:
- Der DMS alleine kann nicht verwendet werden, sondern muss zunächst auf den Prüfling oder die Materialprobe aufgeklebt werden, dessen Verhalten untersucht werden soll. Hierbei ist enorm wichtig, dass eine feste, durchgehende Verbindung zwischen Probe und dem Messgitter des DMS entsteht. Nur dadurch kann sichergestellt werden, dass die Dehnung im Bauteil auch sauber auf den Messstreifen übertragen wird. Sollte dies nicht der Fall sein, kann das zu falschen Ergebnissen und somit wiederum zu katastrophalen Fehleinschätzungen bezüglich des Materialverhaltens führen. Das Gleiche gilt für die Ausrichtung des DMS. Die Dehnung kann nur richtig erfasst werden, wenn die Ausrichtung zur Kraftrichtung passt.
- In der Praxis möchte man z.B. die (mechanische) Spannung messen die in einem Material wirkt oder die Kraft ermitteln die auf ein Bauteil einwirkt. Dazu ist es erforderlich, dass der Dehnungskoeffizient des Prüfmaterials sowie dessen Querschnitt bekannt ist. Daraus läßt sich eine Relation zwischen Kraft, Dehnung und (mechanischer) Spannung im Material herstellen. Dieser Zusammenhang ist wichtig, da über den DMS selbst nur die Verformung (Dehung oder Stauchung) ermittelt werden kann.
- Das jetzt bestehende System muss für die Verwendung noch abgeglichen bzw. kalibriert werden, damit der Effekt der elektrischen Widerstandsänderung richtig verarbeitet werden kann. Dieser Vorgang erfolgt mittels Vergleichen mit einem sogenannten Referenzsystem, dessen Parameter bereits bekannt sind. Ziel ist es, den sogenanten Kalibrierfaktor zu ermitteln, der letzendlich das Verhältnis zwischen der Widerstandsänderung und der Dehnung im Material beschreibt.
- Um die Änderung des DMS letztendlich auszuwerten und somit ein Bauteil beurteilen zu können, ist zudem Software erforderlich, die die vorliegenden Parameter umrechnet. Die elektrischen Signale werden dabei gemäß dem Referenzsystem, bei denen die Informationen zu den gewünschten physikalischen Größen bekannt, sind umgerechnet. z.B. kann mit genormten Gewichten gearbeitet werden, um die entstehende Dehnung in eine (Gewichts-) Kraft umzurechnen.
Hinweis: Die beiden ersten Schritte erledigen im allgemeinen die Hersteller einbaufertiger, DMS-basierter Sensoren, so dass die Nutzung und Bedienbarkeit für den Endanwender deutlich erleichtert ist. In der Forschung und bei großen Bauwerken ist die Verwendung der DMS direkt auf dem zu prüfenden Bauteil aber durchaus üblich – was natürlich erfahrenes Fachpersonal voraussetzt.
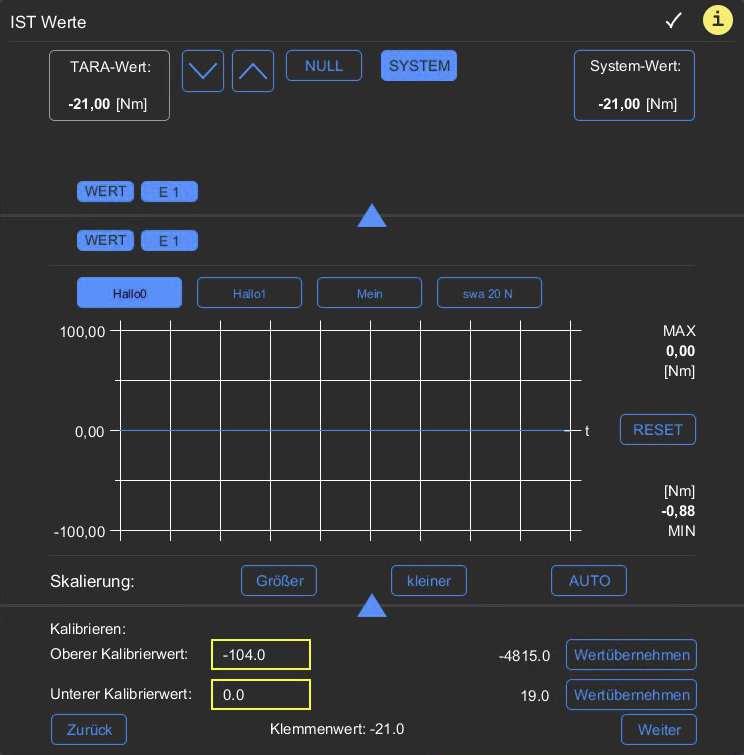
Einsatz von Dehnungsmessstreifen (DMS)
Wie oben beschrieben ermöglicht das Prinzip des Dehnungsmessstreifens eine genaue Messung von sehr kleinen Dehnungen oder Stauchungen, die bei Belastungen in Bauteilen auftreten können. Die Messung ist dabei ein wichtiger Faktor bei der Beurteilung der Stabilität und Zuverlässigkeit von Konstruktionen oder den verwendeten Materialien. DMS-basierte Sensoren sind daher in vielen Anwendungsbereichen weit verbreitet.
Anwendungsgebiete:
- Materialwissenschaftler und Konstruktionstechniker verwenden DMS-Sensoren, um die Materialdehnung und -spannung bei der Entwicklung und Herstellung von neuen Werkstoffen zu messen.
- In der Fahrzeugtechnik werden DMS Sensoren zur Messung der Spannungen und Dehnungen in verschiedenen Bauteilen eingesetzt. Dies umfasst die Messung von Belastungen in Bremsen, Federungen, Getrieben, Motoren und anderen Komponenten.
- In der Medizintechnik wird der DMS Sensor verwendet, um die Dehnungen in Implantaten und Prothesen zu messen. Sie werden auch in der Forschung eingesetzt, um die Belastung auf Gelenke und Knochen zu messen und zu visualisieren.
- In der Luft- und Raumfahrttechnik werden DMS Sensoren zur Messung von Belastungen in Flugzeugen, Raketen und Satelliten eingesetzt. Es wird auch zur Messung von Dehnungen und Spannungen in Bauteilen wie Flügeln, Triebwerken und Fahrwerken verwendet.
- In der Geotechnik wird der DMS Sensor zur Messung von Boden- und Felsdehnungen verwendet. Sie werden auch zur Messung der Spannungen in Bauwerken wie Brücken, Tunneln und Gebäuden eingesetzt.
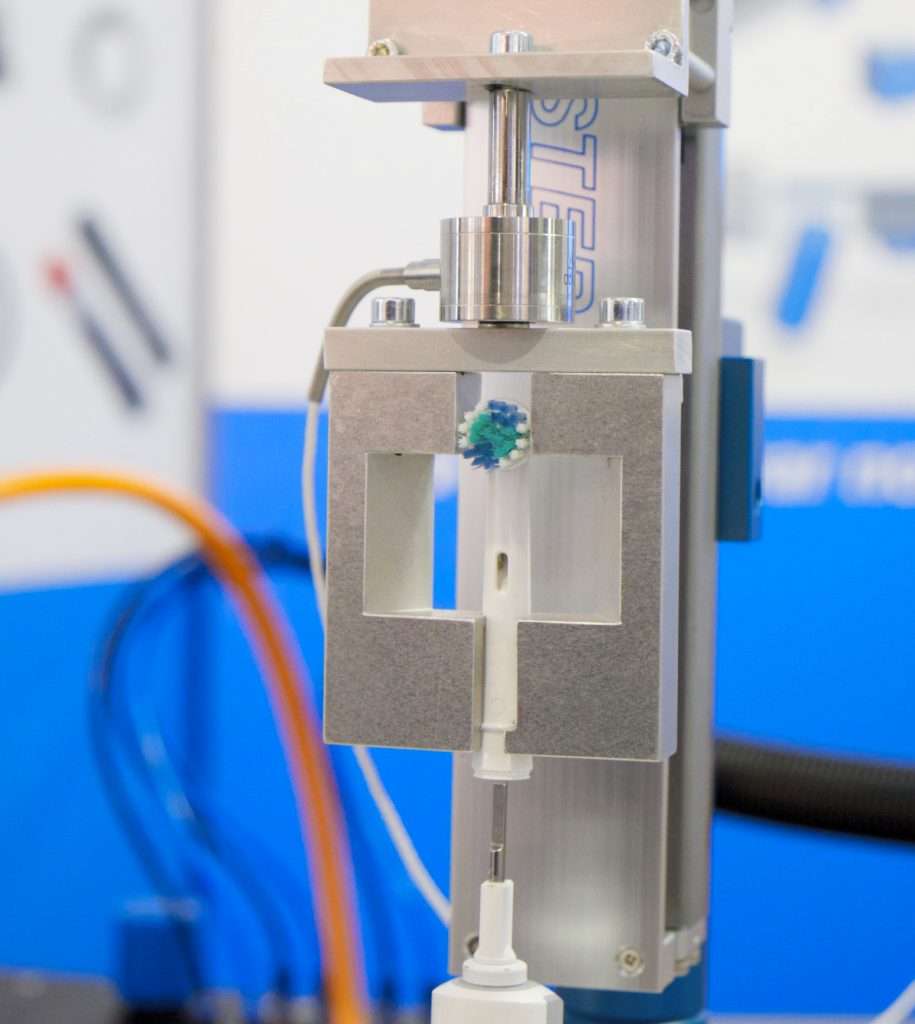
Bauformen und Anwendung in der Prüftechnik
Die zuvor beschriebene Vorgehensweise eine DMS aufzukleben und anschließend auszuwerten findet eher bei physikalischen Experimenten und in der Forschung statt. Grund ist die große Funktionsunsicherheit und die notwendige Erfahrung die im Umgang mit solchen Systemem erforderlich ist. Deutlich praktischer ist der Einsatz von fertig ausfgebauten Sensoren und der dazu passend erhältlichen, standardisierten Messtechnik. Hier kann davon ausgegangen werden, dass etablierte, geprüfte Fertigungsverfahren verwendet werden, die eine sichere Funktion über einen langen Zeitraum hinweg gewährleisten.
Die am häufigsten anzutreffenden Bauformen für DMS sind Sensoren zur Kraft- und zur Momentenmessung. Hier werden die DMS von den Herstellern üblicherweise auf Stahlkörper aufgebracht und anschlussfertig verdrahtet. Sämtliche Technik wird vergossen oder in ein Gehäuse eingesetzt, so dass der Anwender ein solides Produkt in seinem Aufbau verwenden kann.
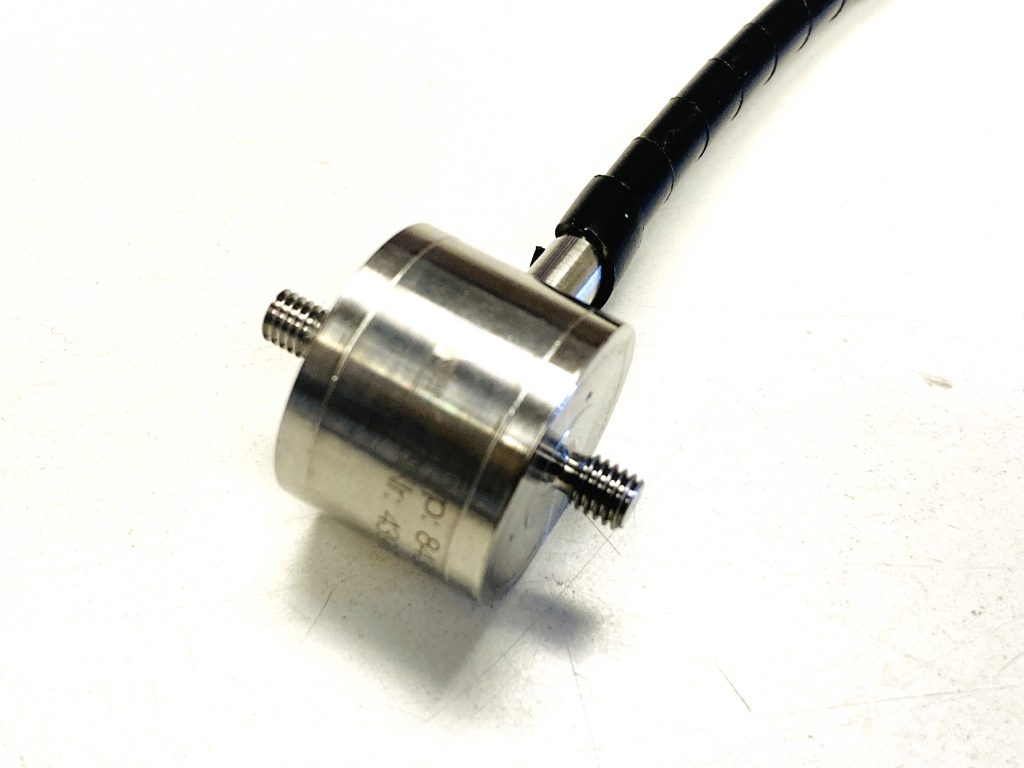
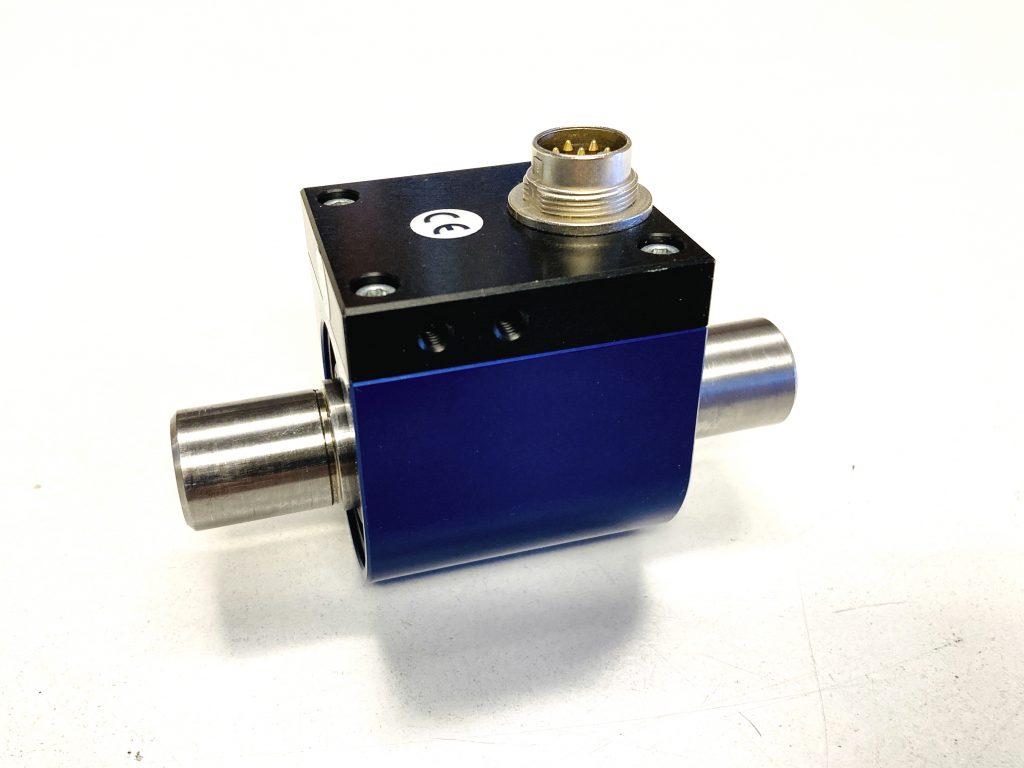
Wertvolle Tipps im Umgang mit DMS (aus der Praxis)
DMS basierte Sensoren sind standardisierte Systeme, von vielen Herstellern erhältlich und gut am Markt verfügbar. Für die Auswahl und die Anwendung von Sensoren können wir aus unserer Erfahrung nachfolgende Tipps zusammenfassen:
- Einsatz von Sensoren nahe am Nennbereich: Jeder Sensor ist für einen bestimmten Arbeitsbereich ausgelegt. Um möglichst genaue Ergebnisse zu erhalten, sollte der Sensor auch bevorzugt in diesem Bereich eingesetzt werden. Zwar können die meisten Sensoren „von Null bis X“ messen, allerdings macht es wenig Sinn z.B. einen 5.000 N Sensor im Bereich von nur 20 oder 30 N einzusetzen. Der Sensor, bzw. die Elektronik wird zwar Werte anzeigen, diese sind aber erfahrungsgemäß nicht sehr genau, da bis zum festgelegten Endwert eine viel zu große Spanne verbleibt. Unsere Erfahrung zeigt, dass die Sensoren in etwa ab der Hälfte ihrer Nennwerte sehr gute Genauigkeiten aufweisen.
- Kalibrieren in die bevorzugte Anwendungsrichtung: Die meisten Sensoren sind vom Hersteller in zwei Richtungen ausglegt. D.h. ein Kraftsensor kann z.B. sowohl in Zugrichtung (positive Werte) als auch in Druckrichtung (negative Werte) genutzt werden. Da sich beide Bereiche elektrisch doch meist etwas unterschiedlich verhalten, empfiehlt es sich den erforderlichen Abgleich (Kalibrieren) in der geplanten Einsatzrichtung durchzuführen. Somit ist sichergestelt, dass das Potential des Sensors bestmöglich genutzt wird.
- Genauigkeitsangaben des Herstellers berücksichtigen: Die erreichbare Genauigkeit wird von den Herstellern meist in Prozent (%) angegeben. Diese Angaben enthalten oft den Zusatz „v.E.“ und bedeuten „vom Endwert“. Das heisst, dass sich die Prozentangabe immer of den größten Messwert bezieht. Beispiel: Die Genauigkeitsangabe auf einen 500 N Sensor beträgt ±1 % v.E.; das bedeutet, dass dieser Sensor auf ±5 N genau messen kann. Was den vorherigen Punkt untermauert, dass ein solcher Sensor z.B. im Bereich 10 N eher grobe Werte liefert, da ±5 N hier eine Toleranz von 50 % bedeuten. Wird der Sensor jedoch in seinem Nennbereich von 500 N benutzt, beträgt die Genauigkeit tatsächlich die angegebenen 1 %.
- Fremdkräfte ausschliessen: Planen Sie Ihren Prüfaufbau so, dass der Sensor nur in die gewünschte Richtung belastet wird. So sollte z.B. ein Kraftsensor nicht mit Querkräften oder Momenten beaufschlagt werden. Diese führen nicht nur zu verfälschten Messergebnissen sondern können auch schnell zur Zerstörung der DMS führen.
- Messketten beachten: Bei der Auslegung von Prüftechnik sollte beachtet werden, dass der Sensor nur ein Teil der Messkette und somit der Gesamtgenauigkeit darstellt. Erfahrungsgemäß verschlechtert eine Messkette von Sensor, Verkabelung, Steckverbinder und Messelektronik die Genauigkeit um den Faktor 10! Das bedeutet, dass der Sensor von vorneherein um den Faktor 10 genauer ausgelegt werden sollte, als die Messaufgabe eigentlich erfordert.
Was man noch beachten sollte
Nach der Auswahl und der Beschaffung sind auch für den Betrieb von DMS-basierten Sensoren einige Hinweise zu beachten. Die Berücksichtigung dieser Punkte hilft Ihre Investition zu schützen und sorgt für einen dauerhaft reibungslosen Betrieb.
- Überlast mit einplanen: Jeder Prüfaufbau wird auf bestimmte Werte hin ausgelegt und auch die Sensorik entsprechend dimensioniert. Es kann aber immer passieren, dass größere Kräfte oder Momente auftreten als geplant – sei es durch ein Versehen oder einfach durch unglückliche Umstände. Damit in diesem Moment ein teurer Sensor nicht zerstört wird, sollten zuvor entsprechende Maßnahmen ergriffen worden sein: Man kann z.B. konstruktiv Sollbruchstellen einbauen oder entsprechende Schutzelemente wie Überlastkupplungen mit vorsehen. Als praktikabel haben sich Sensoren mit eingebautem Überlastschutz erwiesen. Bei diesen ist der innere Aufbau so ausgeführt, dass das System beim Erreichen der Nennlast „auf Block sitzt“ und somit der empfindliche DMS vor Zerstörung geschützt ist. Diese Sensoren weisen meist eine Überlast von 200 bis 500 % der Nennkraft aus, was im allgemeinen einen hinreichenden Schutz darstellt.
- Auf Kabelschutz achten: Oftmals besitzen Prüfaufbauten bewegte Teile. Achten Sie also darauf, dass die empfindlichen Kabel nicht geqeutscht oder überlastet werden. Vielfach sind die Kabel auch nicht für hohe Bewegungszyklen ausgelegt – in diesem Falle empfiehlt es sich ein sogenanntes schleppfähiges Kabel vorzuschalten und das eigentliche Sensorkabel fest zu verlegen. Ein zusätzlicher Steckverbinder birgt allerding lieder die Gefahr, dass eine Signalverschlechterung auftritt.
- Regelmäßige Kalibriervorgänge einplanen: Um dauerhaft zuverlässige Werte von einem Sensor zu erhalten, empfiehlt sich der regelmäßge Abgleich mit einem Referenzsystem. Als gut praktikabel hat sich eine jährliche Überprüfung erwiesen. Diese Aufgabe übernehmen oftmals auch externe Dienstleister. In diesem Falle brauchen Sie keine eigenes, teures Equipment anzuschaffen.
- Extratipp: Planen Sie von vorneherein ein entsprechendes Budget und Stillstandzeiten für die tournusmäßige Überprüfung. Die Kosten können hier je nach System von mehreren hundert bis hin zu tausenden Euro liegen.
Unser Fazit:
DMS-basierte Sensoren sind vielseitige Messinstrumente, die in vielen
Branchen eingesetzt werden. Das Prinzip und die Struktur des Sensors ermöglichen eine genaue Messung der Dehnungen im Material und
lässt sich mit entsprechender Elektronik und Software gut auf die gewünschten physikalischen Größen zurückführen. Die Anwendungsbereiche reichen von Materialwissenschaften bis hin zur Luft- und Raumfahrttechnik. Der DMS-basierte Sensor ist somit ein wichtiger Bestandteil bei der Entwicklung und Herstellung von Produkten und Werkstoffen.
Für weniger erfahrene Anwender ist es hilfreich auf fertig konfigurierte Systeme zurückzugreifen um Unsicherheiten und Fehlfunktionen so weit wie möglich auszuschließen. Da es sich um erprobte und etablierte Technik handelt, sollte es dabei zu wenig Problemen kommen und die Systeme sollten sich gut in die Bereiche der Prüftechnik und der Qualitätssicherung einfügen lassen.
Nützliche Links
Dehnungsmessstreifen und Brückenschaltung detailliert erklärt:
Sensoren zur Kraftmessung oder Momentenmessung:
Auswertung von DMS mit entsprechender Messelektronik: